固态电池与液态锂电池在产业链上具有相似性,两者的核心差异在于中上游的负极材料和电解质。
在之前的文章中,我们介绍过固态电池最大的变化环节---固态电解质,可以点击文章链阅读了解:
今天,重点来聊一下固态电池新一代负极材料--硅基负极。
负极材料预计将经历从石墨向硅基负极、含锂负极,最终升级为金属锂负极的演变过程。
当前,石墨负极的开发已接近其理论极限,锂离子电池性能要求不断提升,传统石墨负极正面临着被逐步取代的趋势。
硅基负极材料具有高能量密度和出色的快充性能,将成为固态电池当前负极材料的理想选择。
随着固态电池等新型电池技术的规模化应用逐步展开,硅基负极材料大有可为。
关注【乐晴行业观察】,洞悉产业格局!
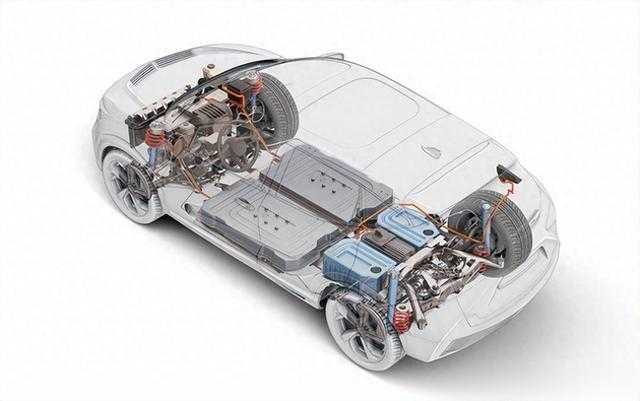
硅基负极材料行业概览
随着电芯技术的重心逐渐从“降本”向“增效”转移,现有材料体系的电芯技术发展遇到瓶颈。只有在下一代高性能电芯上取得性能或成本优势,才能巩固电池行业的领先地位。
硅基负极材料兼具“高容量+高工作电压+低成本”的特点。
从中长期提升能量密度的角度来看,材料厂商更倾向于发展硅碳负极,尤其是采用气相沉积法制备的硅碳材料。
硅基负极材料以其高达4,200mAh/g的理论比容量远超石墨类负极材料,在能量密度和续航能力优势凸显。
据预测,到2025年全球硅基负极材料市场的整体规模有望达到300亿元,行业空间十分广阔。
![]()
在硅基负极材料的技术路径中,硅氧和硅碳是主要的研发方向。
目前市场上以硅氧负极为主,主要原因是贝特瑞、杉杉股份等企业的氧化亚硅产品成熟度较高。但是,硅氧负极仍需要在首效和能量密度方面进行提升。
此外,硅基负极材料结合了碳材料的高电导率、稳定性以及硅材料的高容量特性,当前正引领着固态电池负极材料行业的发展方向。
目前商业化的硅基负极材料主要有四种类型:碳包覆氧化亚硅、纳米硅碳、硅纳米线以及无定型硅合金。
尽管硅碳负极的循环性能相较于硅氧负极稍弱,但目前已通过降低纳米硅粒径等方法来提升其循环性能。不过,传统研磨法产出的粒径仍受限于100nm。
![]()
硅基负极材料产业链梳理
硅基负极材料产业链的上游关键原材料包括石墨、二氧化硅、硅合金、碳源气、锂盐等。中游环节聚焦于硅基负极材料本身。下游硅基负极材料被广泛应用于各类场景中,包括动力电池、储能电池和消费电池等。
从下游应用角度来看,硅基负极材料已被宁德时代麒麟电池和特斯拉4680电池所采用。
特斯拉一直推广的4680大圆柱电池体系中,硅基负极被视为提升性能的关键组成部分,并已成功实现在Model 3车型上的装车应用。
下游负极材料厂商包覆材料的认证周期通常持续6至12个月,并且对供应商的产能规模、供应保证能力以及批次稳定性等方面都有着严苛的要求。
硅基负极产业链图示:
![]()
硅基负极材料产业竞争格局和龙头梳理
据EVTank数据,2023年国内锂电负极材料市场中,出货量排名前四的厂家合计占据了市场的57%份额,市场具有高度集中性。前四的厂商分别为贝特瑞、杉杉股份、江西紫宸和中科星城。贝特瑞在2023年的负极市场占有率约为22%,相比2022年,CR3的占比略有下滑。
此外,近年来涌现出的广东东岛、河北坤天、金汇能、碳一、青岛科硕等厂商,在负极材料生产方面也取得了显著突破,年产能已突破2万吨大关。
2023年中国锂电负极竞争格局:
![]()
具体到硅基负极材料方面来看,国内主流负极材料企业包括贝特瑞、杉杉股份、璞泰来、胜华新材、国轩高科、凯金能源、硅宝科技、天目先导、兰溪致德等均在积极建设硅基负极材料产能。
由于硅基负极技术存在着较高的技术壁垒,当前量产厂商数量相对较少,多数厂商仍处于中试阶段。
有一些国内厂商在这方面取得了显著进展,兰溪致德在22年的时间内已成功实现硅碳负极产能超过2000吨,并且正在建设一期8000吨的硅碳负极产能;贝特瑞目前已拥有5000吨的年产能,同时正在筹建年产能高达4万吨的生产线。
国内亿纬锂能、中创新航以及蜂巢能源等头部电池企业已经率先进行了硅基负极高能量密度电池的产能布局,以应对未来市场对高性能电池的不断增长需求。
部分电池企业布局硅基负极:
![]()
结语
自2023年下半年起,“负极掺硅”高性能动力电池在装车应用方面持续受到热捧。国内车企蔚来、智己、埃安等知名汽车品牌已开始为其旗下车型配备硅基负极动力电池。随着下游电池企业对搭载硅碳负极的高密度动力电池产品需求量的不断扩大,预计硅碳负极材料的需求将会迎来高速增长。这一趋势将为具备量产能力的硅基负极材料厂商带来广阔的市场机遇。
关注【乐晴行业观察】,洞悉产业格局!
转载此文是出于传递更多信息目的。若来源标注错误或侵犯了您的合法权益,请与本站联系,我们将及时更正、删除、谢谢。
https://www.414w.com/read/115073.html