正极材料短期沿用高镍体系,长期向超高镍、富锂锰基、高压尖晶石等材料迭代。固态电池电化学窗口更宽,因此可以使用的正极材料更为广泛。半固态/固态电池短期预计仍会沿用三元高镍体系,但或通过单晶化、氧化物包覆、金属掺杂等手段进一步提升电压,从而提升电池能量密度。在固态电解质、金属锂负极等技术逐渐成熟后,正极材料预计向超高镍、富锂锰基、高压尖晶石等新型体系进一步迭代。
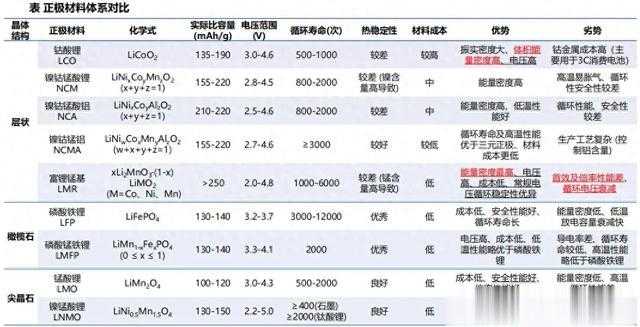
固态电池正极:镍锰酸锂兼具电压及成本优势,富锂锰基高比容优势明显
尖晶石镍锰酸锂兼具较高比能、低成本及高安全,难点在于稳定高压正极的界面。镍锰酸锂为尖晶石结构,稳定性优于层状氧化物,且具有三维Li+扩散通道,倍率性能良好。镍锰酸锂以镍均匀取代锰酸锂中25%的锰,工作电压高达4.7V,使比能量超越635Wh/kg,接近三元,远高于铁锂,且其为低镍无钴二元正极,成本优势显著。镍锰酸锂的难点在于材料电压平台过高(5V)而导致正极界面不稳定,可通过金属掺杂、氧化物包覆及铁锂、三元正极复合等路径解决。
富锂锰基具备极高比容、高电压及成本优势,预计主流应用路线为正极材料复合。富锂锰基电压窗口宽(2.0-4.8V),常压下循环稳定性优于其他商业化正极,高压放电比容量可达250mAh/g以上,与硅碳负极匹配,电芯能量密度有望超越400Wh/kg,且其为低镍高锰正极,低瓦时成本媲美磷酸铁锂。但富锂锰基电子电导率极低(~10-8S/cm) ,高压下循环过程中易发生尖晶石相变,且高压电极/电解质界面副反应严重,面临倍率性能差、首次库伦效率低(<80%)、循环容量及电压衰减等难点,短期无法单一使用,可与现有三元、钴酸锂、磷酸铁锂等正极混合降低电压,提早实现商业化应用。
![]()
干法电极工艺:与全固态电池相容,粘结剂更换为PTFE等材料
干法工艺是未来电极工艺的迭代方向,优势是提升生产效率、降低成本,难点在于混合均匀,粘结剂更换为PTFE等材料。传统湿法电极工艺存在成本较高、工艺复杂、NMP溶剂有毒等问题,而干法电极工艺是一种无溶剂化的生产技术,使用高剪切和/或高压加工步骤来破碎和混合材料,电极膜结构形成更厚,粘结剂则以纤维状态存在,不会阻碍电子和离子传导,导电性好,节省了材料、时间和人工等生产成本。但其难点在于市售的粘结剂颗粒较大,难以均匀分散,进而造成了干法电极良品率低等问题。
半固态电池仍以湿法电极工艺为主,而全固态电池需更换干法电极工艺。成膜工艺是固态电池制造的核心,不同的工艺会影响固体电解质膜的厚度和离子电导率。半固态电池中,材料体系变化有限,因此主要使用传统湿法电极工艺。而全固态电池中,硫化物电解质对极性有机溶剂极为敏感,同时金属锂与易于溶剂反应,此外膨胀更加严重,传统的PVDF-NMP体系粘结强度有限,而干法电极中由PTFE原纤维化构成的二维网络结构,可以抑制活性物质颗粒的体积膨胀,防止其从集流体表面脱落,预计主要使用干法电极工艺。
![]()
制造/封装方式:全固态电池向叠片+软包的方向迭代
正极、电解质和负极的复合过程,是固态电池制备的关键工序,其中温等静压为重要复合方式。固态电池可将电极单元直接堆叠内串,因此无需内部极耳,从而提高制造效率,降低包装成本。但一体化叠片存在固-固界面接触问题,需通过施加压力等手段来进行改善。传统辊压等方法可能导致颗粒的重新堆积与变形,目前一种优选的方法是采用等温静压法,一般温度在80-120℃,压力在300MPa左右,利用气/液体介质均匀传递压力的性质,从各个方向对试样进行均匀加压,进而获得坚实的坯体,预计在固态电池领域有较大发展。
全固态电池向叠片+软包的方向迭代。与液态锂离子电池相比,固态电池后段工序不需要注液化成,但需要加压或者烧结;制造/封装方式看,氧化物及硫化物电解质柔韧性较弱,更适用于叠片工艺,其内部变形、弯曲或断裂的概率低,此外软包封装在能量密度上也具备优势,可容忍充放电过程中的体积变化,因此叠片+软包的封装方式最适合于固态电池。
![]()
注:本站转载的文章大部分收集于互联网,文章版权归原作者及原出处所有。文中观点仅供分享交流,如涉及版权等问题,请您告知,我将及时处理!
转载此文是出于传递更多信息目的。若来源标注错误或侵犯了您的合法权益,请与本站联系,我们将及时更正、删除、谢谢。
https://www.414w.com/read/515137.html