在高度依赖模具的生产环境中,模具管理与APS生产排程的有效整合是提升效率、确保订单交期的关键。以下是针对模具管理的几个核心策略,通过APS高级计划排程系统的辅助,实现产能优化与生产调度的智能化升级:
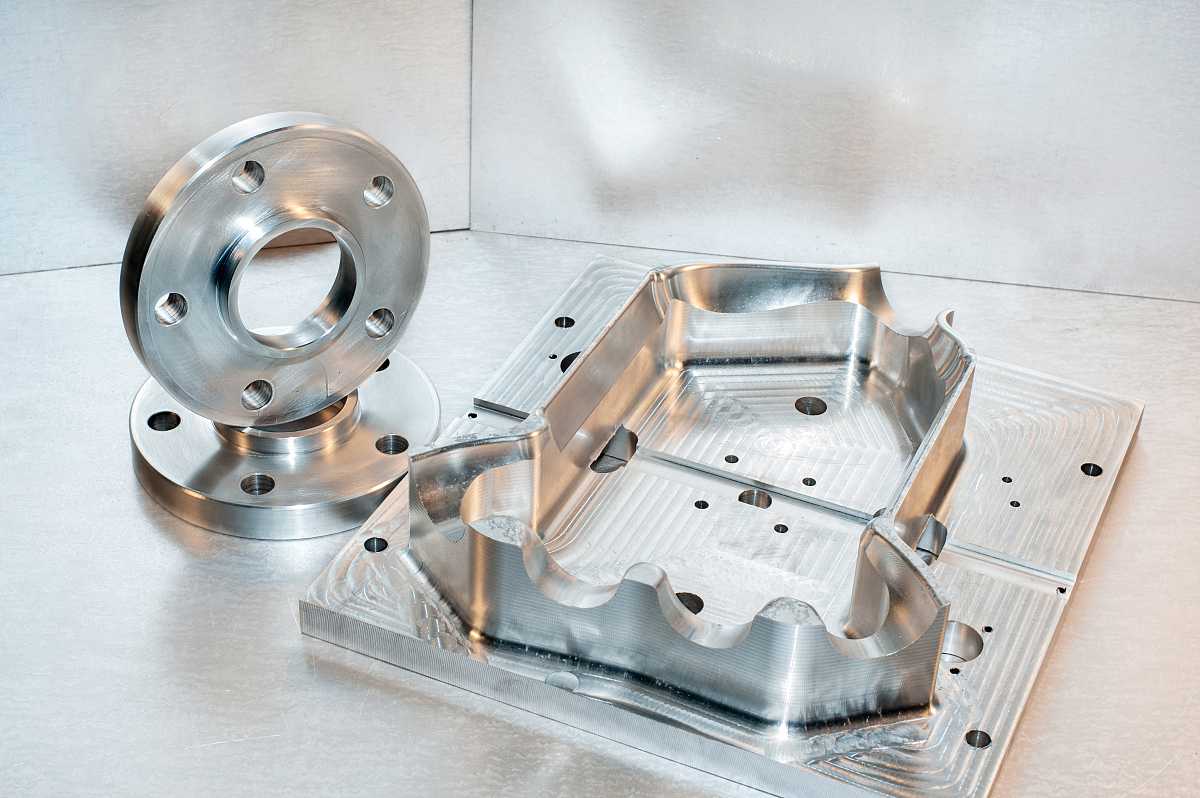
模具管理系统
模具数量与产能预估
模具的持有量直接映射为生产线的潜在产能。通过精确计算模具数量,企业能够合理预测各工序的最大生产能力,并据此为产品设定合理的交货期。APS系统在此基础上进一步分析,在订单洪峰来临时,评估新增模具的可行性,确保不仅能覆盖新增模具的成本(包括采购与维护),还能有效缩短客户等待时间,实现经济效益与市场响应速度的双赢。
![]()
图APS-物料模具绑定示例
模具智能分配策略
面对模具共模与互换镶件的复杂场景,APS系统通过算法优化模具分配逻辑。一方面,系统自动识别共模机会,合并相似订单工序,最大化模具利用率,实现多订单的同时满足;另一方面,依据订单优先级、交期紧迫程度及物料到货时间等因素,动态调整模具分配优先级,确保关键订单得到优先处理,在保障生产灵活性的同时,也优化了资源分配的合理性。
模具寿命监控与维护规划
结合模具管理系统数据,APS系统实时监控模具的使用状态与剩余寿命,根据MES系统反馈的工序信息,智能规划模具的轮换时机,避免过度使用导致的产品质量问题和模具损坏。系统还将主动提醒生产部门进行模具维护或更换,确保生产连续性与产品质量的稳定性,延长模具的使用寿命。
模具效能分析与决策支持
![]()
图APS-模具瓶颈示例
![]()
图APS-模具使用情况示例
基于APS生成的产品工序生产计划,APS系统进一步提炼工序内每日的模具使用报告,详尽展现模具在各生产环节的应用情况及潜在瓶颈。这些数据不仅为模具的补充采购提供了决策依据,还指导产品设计部门对工艺流程的持续优化。决策部门可依此调整模具投资策略,聚焦于提升生产效率和降低整体成本,实现精益生产的目标。
转载此文是出于传递更多信息目的。若来源标注错误或侵犯了您的合法权益,请与本站联系,我们将及时更正、删除、谢谢。
https://www.414w.com/read/680939.html