世界首座电热熔盐储能注汽试验站在辽河油田建成投产,我国自主研发的电热熔盐新型储能注汽技术实现“从0到1”的突破。
辽河油田作为国内最大稠油高凝油生产基地,连续37年保持油气千万吨规模稳产。据悉,该油田注汽系统年消耗天然气约14亿方,排放二氧化碳303万吨,高能耗、高碳排的现状与绿色转型高质量发展的矛盾,亟须通过探索清洁能源替代的有效途径加以解决。同时,加快提升绿电消纳能力,为电网削峰填谷提供技术支持,也是辽宁省绿色能源升级发展的现实需求。
01熔盐储能技术的关键是硫磺原料的确定性
据介绍,现有熔盐储能技术是利用熔盐高热容、高分解温度、高流动性、低腐蚀性的特点,将其作为储热和传热工质,把光热或谷电、绿电转化为热能储存在熔盐中,再通过全天连续释放热能产生过热蒸汽用于发电,以解决新能源随机性、间歇性、波动性产能与连续性用能的矛盾,为生产提供稳定的清洁能源供应。
02晋盛开发的硫膏深加工技术可为熔盐储能提供廉价原料
目前,由晋盛智能开发的硫膏深加工技术克服了硫膏存在的焦油、煤灰、各种有机物容易堵塞管道的问题,精确掌握了硫膏熔融后的顺畅流动技术,以及除渣后的无害化处理,废水的合理处理与去向,废气的治理等一系列次生污染问题,成为行业内率先解决这些疑问题的公司之一。如果此次技术成功实现产业化,将会让每吨熔盐产品成本再降500--800元左右。以此提高储能企业的市场竞争力,推动储能企业的可持续性发展,也让硫膏产生企业找到了污染治理的新路子。
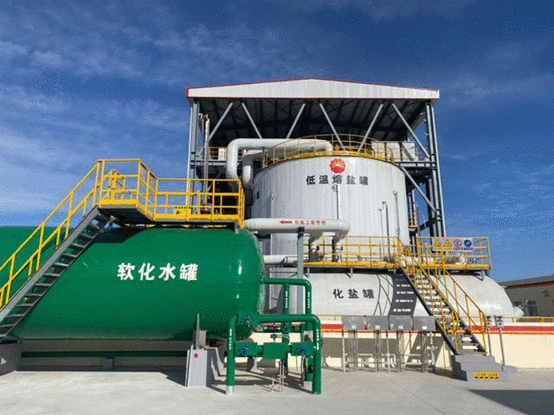
03国内首次将电热熔盐技术应用油田生产注汽系统
辽河油田电热熔盐储能注汽试验站项目是国内首次将电热熔盐技术应用油田生产注汽系统,也是辽宁省重点“揭榜挂帅”项目。“相较于以往综合效率约为35%的熔盐蒸汽发电系统,辽河通过独创研制的蒸汽发生系统将回用软化污水与高温熔盐换热产生8MPa、295℃、干度80%的湿饱和蒸汽直接用于油田注汽生产,有效减少能量的过程消耗,综合效率可达到90%,是突破该领域技术应用场景的一次全新尝试。
![]()
04未来将实现大规模减少化石能源消耗
据悉,随着该项目的顺利投产,未来将实现大规模减少化石能源消耗,替代当前辽河油田蒸汽辅助重力泄油技术(SAGD)、蒸汽驱等连续运行的常规燃气注气站,每年可替代蒸汽1600万吨,消纳谷时电、绿电108亿度,实现天然气减耗10.4亿方,二氧化碳减排225万吨。同时,该项目将为提升电网灵活调节能力,促进辽宁省能源供需平衡,实现风光弃电量、弃电率双降提供重要技术支撑。
![]()
转载此文是出于传递更多信息目的。若来源标注错误或侵犯了您的合法权益,请与本站联系,我们将及时更正、删除、谢谢。
https://www.414w.com/read/420197.html