“促进模具产业向深层次数字化、信息化制造的方向发展,而金属3D打印技术作为具有代表性的增材制造技术,与模具制造有着共同的产业特征,正在成为模具高效、高精度制造的新关键技术。”
——中国模具工业协会
《模具行业“十四五”发展纲要》
金属3D打印技术在模具制造中的一项重要应用就是制造注塑模具。注塑过程一般包括:加料、塑化、注射、冷却、脱模,其中冷却时间约占产品成形周期的50%~80%。可以说,注塑模具冷却系统直接影响了塑件质量和生产效率。
注塑模具冷却系统
冷却系统通常是在模具内开设冷却水路,利用循环流动的冷却水实现温度控制,以满足注塑工艺要求。
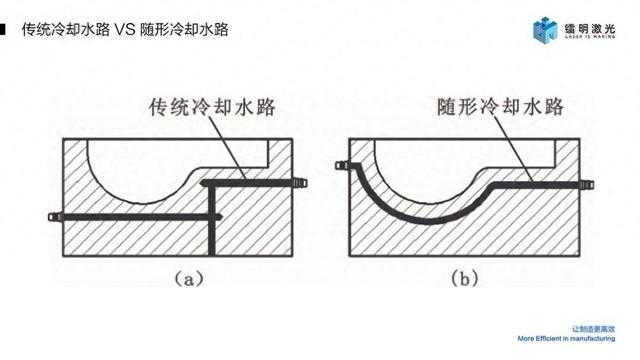
传统加工方式下,水路只能为圆柱形直孔,无法完全贴近注塑件表面。但依托金属3D打印技术,可突破传统加工限制,实现随形冷却水路设计制造,在合理区间内可任意设计弯曲水路、水路截面可设计成任意形状、水路走向可根据型腔表面轮廓变化而变化,达到更快速、更均匀的冷却效果,改善注塑件的质量,减少注塑成形周期。
应用案例
随形水路USB上盖模仁案例
![]()
![]()
该USB上盖模仁的原始设计中,公模内部无水路,只有母模有水路,最终注塑件成形周期为30s;
![]()
使用金属3D打印技术制造该模具时,在公模仁内部设计随形冷却水路,水路直径?0.89mm、壁厚0.8mm,最终将注塑件成形周期缩短至20s。
![]()
![]()
随形水路连接器模仁案例
经过随形水路设计优化,使用金属3D打印技术制造该模具,最终注塑件成形周期由22s减少至12s,成形周期缩短45%。
![]()
随形水路浇口套案例
金属3D打印技术可实现大部分的注塑模具制造,但综合考虑成本与效率,也会采用打印部分镶件、模仁的方式,如:浇口套、斜顶、模仁垫板、后模镶件、前模镶件、滑块等。
![]()
上图为使用金属3D打印技术制造的随形水路浇口套,在注塑成形过程中有效增强冷却效果:冷却时间由25s缩短至5s、注塑件成形周期由37s缩短至15s,成形周期减少60%,注塑件成形质量良好。
![]()
金属3D打印水路模仁
下图中的模仁由金属3D打印一体成形制造,经过热处理及传统机加工后投入使用。
![]()
打印材料:不锈钢SUS420,硬度HRC 48-52、抛光等级可达至A1,可满足透明件需求
打印时间:30小时/个(不包含热处理和机加工时间)
转载此文是出于传递更多信息目的。若来源标注错误或侵犯了您的合法权益,请与本站联系,我们将及时更正、删除、谢谢。
https://www.414w.com/read/75886.html