随着新能源汽车市场占有率的逐年增长,相关研究也日趋成熟。新能源汽车包括纯电动、增程式电动、混合动力、燃料电池电动、氢动力及各类新型电动汽车,它们共同推动了减少对非可再生资源依赖的进程。因此,新能源汽车的发展已成为汽车行业的新趋势。作为新能源汽车产业化的重要技术之一,电机绕组端部的灌封保护对于提升电机的可靠性和效率至关重要。理想的灌封胶应具备高导热性、良好的流动性、耐开裂性和强粘结力等特点。
尽管市场上对于新能源汽车电机用的高导热低黏度灌封胶研究相对较少,相关产品也较为稀缺,但导热型灌封胶的研究在国内外并不少见。然而,这些研究主要集中在小尺寸电子元器件的灌封上,其常规产品普遍存在黏度较高、流动性差、密度大的问题,这使得它们在汽车电机上的应用存在困难,不仅增加了汽车的重量,还可能导致能耗比过高。另一方面,尽管有关于低黏度型灌封硅胶的研究,但这些产品在导热性方面并未得到很好的平衡。
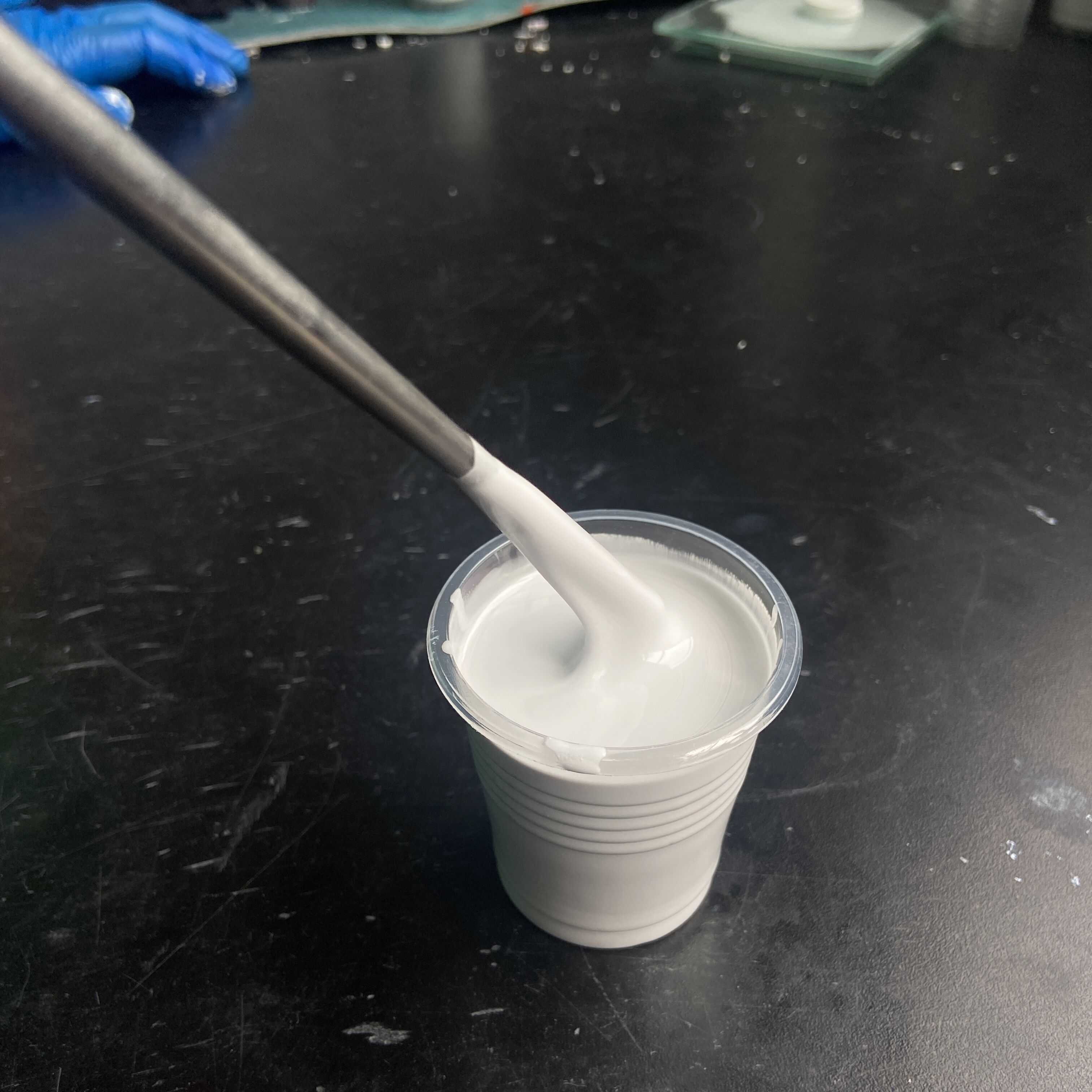
本研究重点在于开发一种适用于新能源汽车电机的高导热低黏度灌封胶用导热粉。为此,研究团队采用了一系列材料和制备工艺,包括环氧树脂、阻燃稀释剂、氧化铝、氢氧化铝、氢氧化镁、硅烷偶联剂等,并通过强力搅拌和真空脱泡等步骤,制备出了A组分。同时,固化剂如聚氧化丙烯基二胺和氨基乙基哌嗪等被混合为B组分。在60℃下加热A组分,然后加入B组分,在80℃下固化2小时,随后缓慢降温,得到了灌封胶固化物。
研究结果表明,导热粉填料的加入显著降低了灌封胶的固化收缩率,并提高了其耐开裂性能。当导热粉填料加入量达到260份时,固化收缩率降至1%以下。此外,不同粒径的氧化铝复配填料不仅提高了灌封胶的热导率,还提升了其力学性能,同时降低了黏度。采用阻燃剂复配方法,阻燃剂的用量可减少至30份,达到V-0级阻燃要求,并进一步降低黏度。在偶联剂的使用上,硅烷偶联剂的加入量为主体树脂质量的5%时,树脂黏度趋于稳定,而KH560体系中填料的加入使得灌封胶的黏度下降最快并趋于稳定,且稳定后的黏度最低。
![]()
灌封胶导热粉体材料
最终,研究团队成功制备出了一种新型高导热低黏度灌封胶用导热粉体材料,其性能最佳,该粉体对新能源汽车电机定子导热灌封胶具有良好的粘结性和耐开裂性,能够满足新能源汽车电机工装的要求。
在动力电池的应用中,导热灌封胶扮演着提升电池散热效率、增强抗震防护性能、延长电池寿命及耐久性的重要角色。尽管如此,导热灌封胶在实际应用中仍面临挑战。主要问题包括:
1. 流动性不足:流动性较低的导热灌封胶在相同导热系数下,难以充分填充元器件间的细小缝隙,导致界面处空气积聚,从而增加整体热阻,影响散热效果。
2. 抗沉降性差:导热灌封胶的抗沉降性能不佳,易形成硬结块,这不仅增加了加工成本,还可能导致导热不均匀,影响电池散热性能。
为解决这些问题,导热粉体的选择至关重要。东超新材已研发出适用于不同性能需求的导热灌封胶专用粉体,以满足行业需求。
转载此文是出于传递更多信息目的。若来源标注错误或侵犯了您的合法权益,请与本站联系,我们将及时更正、删除、谢谢。
https://www.414w.com/read/731010.html