电子发烧友网报道(文/梁浩斌)前段时间在村田的媒体交流会上,我们了解到了村田推出的一种“埋容”方案。以往的电容都需要贴片到主板或者芯片基板上,而村田推出了一种创新方案,将电容集成到PCB内部,无须与传统封装一样占据PCB表面空间,村田称之为Integrated Package Solution(内置埋容解决方案)。
内置埋容采用了叠层工艺,实际上也是与贴片电容一样,是由不同层和不同材料组合的产品。而其中一个特点是通孔,可以直接连接埋容的顶部和底部电极,埋容电容内部有许多通孔结构,这样的结构可以实现垂直供电,缩短封装内供电距离,从而降低损耗。
实际上,除了电容之外,功率器件也有嵌入到PCB内的封装。
功率器件嵌入到PCB有什么好处
以功率模块为例,目前在电动汽车主驱逆变器上的功率模块,基本上是注塑式或是框架式封装。由于功率芯片在工作时会产生大量的热量,因此大多数都使用高导热和电气绝缘的基板,将功率芯片焊接在基板上,比如覆铜陶瓷基板等,以实现良好的芯片散热。
这种基于陶瓷基板的功率模块,其中的芯片只能通过陶瓷表面覆铜进行单层布线,并采用架空键合线等方式实现电路连接,这种连接方式使得电气性能和散热受到了很大的限制,特别是降低换流回路和栅极控制回路的杂感和芯片间的热耦合方面。
纬湃科技此前在一场研讨会上表示,在电气性能方面,PCB具有天然的优势,比如可以进行多层布线,通过控制线间距及层间距减少EMC的影响;PCB使用的绝缘材料可以满足400V至1000V高压绝缘的要求;埋入PCB的电子器件可以通过高散热材料和合理的散热层设计达到优秀的散热性能。因此PCB嵌入功率芯片的技术用于功率模块封装具有极大的性能潜力。
根据纬湃的技术评估数据,首先在通过电流的能力上,传统封装的功率模块大概是每29平方毫米芯片101A,而PCB嵌入式功率模块中每29平方毫米芯片是142A,单位通流能力提升约40%,这也意味着相同电流输出的情况下,功率芯片用量可以减少三分之一。在相同的功率输出要求下,功率模块的物料成本可以降低20%。
具体到逆变器的应用中,以800V逆变器、采用SiC功率芯片为例,逆变器采用嵌入式封装SiC模块后,相比采用框架式封装的SiC模块,逆变器的WLTC循环损耗减少60%,同时还能降低逆变器尺寸。
对于主驱逆变器,一个比较重要的指标是可靠性和使用寿命,纬湃科技目前已经开发了基于400V和800V系统采用PCB嵌入式封装的SiC模块样品,而对样品进行的AQG324关键可靠性验证中显示,PCB嵌入式封装的设计寿命可达传统封装的数倍。其中800V的SiC模块样品中,每个功率开关使用了8颗面积为20平方毫米的功率芯片,半桥PCB尺寸为70mm×40mm,模块杂散电感1nH以下,压摆率超过每微秒25kV,单相输出电流峰值有效值达到850A。
PCB嵌入式封装的实现方式
要将功率器件嵌入到PCB内,对PCB的材料和制造工艺也提出了更高的要求,比如需要PCB材料需要具备良好的热导性,能够承受高电压和大电流,同时具有低电阻和低寄生电感特性,以减少功率损耗;PCB材料还必须具有良好的绝缘性能,以确保器件之间的电气隔离,防止短路和击穿等。因此也需要PCB厂商的密切配合才能实现大规模量产的PCB嵌入式封装功率器件。
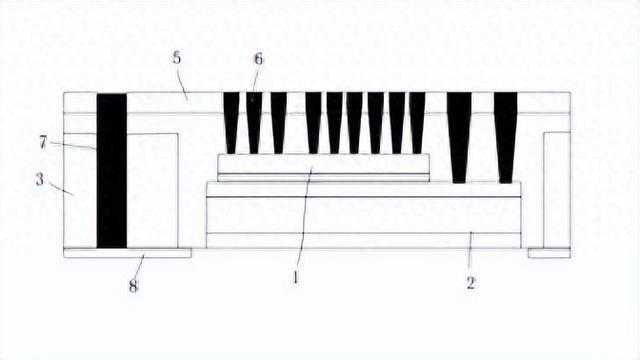
深南电路封装专利示意图 来源:专利之星CN 118173455 A
今年2月,深南电路申请了一项名为“一种功率芯片埋入式的封装基板及封装方法”的专利,并在6月公开。如上图所示,1是裸芯片、2是刚性衬底、3是第一芯板、4是绝缘层、5是第一外连金属层、6是金属层表面盲孔、7是连接柱、8是第一内连金属层。
在这份专利中描述了这种封装的步骤:首先获取第一芯板,在第一芯板上开设沿厚度方向贯穿的通槽;将裸芯片固定在刚性衬底上;将裸芯片和刚性衬底整体嵌入到第一芯板的通槽中;在第一芯板上压合绝缘层,绝缘层覆盖通槽内的裸芯片;在绝缘层上形成第一外连金属层;从第一外连金属层的表面加工多个盲孔,盲孔实现裸芯片和刚性衬底与所述第一外连金属层三维垂直互联,使得裸芯片直接通过盲孔扇出信号,减小信号传输路径,降低传输损耗。裸芯片封装在第一芯板内,为第一芯板表面释放空间,能够贴装更多电子元器件,减小封装体的占用空间。
![]()
除了嵌入PCB之外,2022年的时候,中科院微电子所侯峰泽副研究员和复旦大学樊嘉杰青年研究员也提出了一种基于基板埋入技术的新型SiC功率模块封装及可靠性优化设计方法:采用新型光敏成型介质(PID),通过光刻工艺制备SiC MOSFET功率器件电极上的互连盲孔;基于板级物理气相沉积(PLPVD)技术批量更改SiC MOSFET等功率器件电极上的金属;通过双面再布线层(DSRDL)工艺替代功率器件的传统键合技术。
最终效果从上图b可以看到,基板埋入封装体积远远小于TO-247封装的分立器件。
小结
功率器件采用PCB嵌入式封装后,电路布局设计相对于传统封装更加灵活,能够极大提高开发效率。同时也能大幅缩小整体系统体积,比如在逆变器中的应用,同样输出功率需求下,降低功率芯片用量,为系统带来整体的成本效益。还有另一个好处是,一些高级电路拓扑,如三电平、IGBT/SiC MOSFET混并等方案,由于结构较为复杂、采用元器件数量较多,传统封装在电动汽车逆变器领域还应用较少,但未来通过更灵活的PCB嵌入式封装,可能会推动这些拓扑在主驱逆变器领域的应用落地。
转载此文是出于传递更多信息目的。若来源标注错误或侵犯了您的合法权益,请与本站联系,我们将及时更正、删除、谢谢。
https://www.414w.com/read/1199361.html