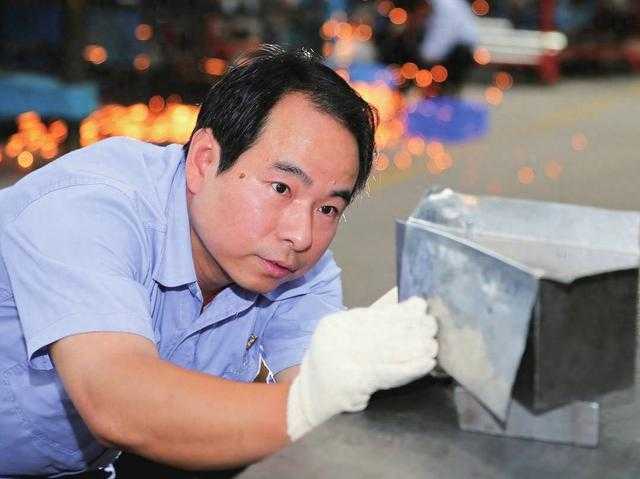
黄卫始终扎根飞机制造生产一线,坚持在运8、运9系列飞机弹簧、导管、焊接件等关键零件生产中破解一道又一道技术难题,在岗位攻关中完成一项又一项生产任务。
中国航空工业集团特级技能专家、航空工业陕飞钳焊厂钳工高级技师黄卫说:“创新让我乐在其中,为推动航空产业装备制造高端化、智能化发展,我将永不停步。”他还获得中国航空工业集团公司特级技能专家、技术能手,陕西省“首席技师”“三秦工匠”“工人发明家”,汉中市“天汉工匠”等称号。
“新挑战、新任务、新问题面前,该如何应对?”黄卫的选择是“哪里有困难,我就去哪里”。平日里,他爱“琢磨”,也爱“凑热闹”,车间里只要出现焊接、设备改造、技术革新等方面的问题,他总会凑到跟前认真听、详细记、不停问,有时下班回家还要整理归纳、继续学习。
随着科研任务中新工艺新材料的广泛应用,身为技能专家的黄卫又有了新想法。他利用专业理论知识,将新工艺、新任务与工作实践紧密结合,先后攻克了双曲面不锈钢零件褶皱排除、大直径钢丝弹簧数控绕制、大直径导管数字化制造、异形导管自动化焊接等一个个制约生产发展的技术难题。
面对搅拌摩擦焊接技术完成飞机超大壁板零件焊接的艰巨任务,他带领团队主动出击,提前介入新设备认真分析新工艺,提出多种工艺方案并反复开展试验,最终攻克了超长零件对接组焊误差小于0.1毫米的加工难题,探索出一整套加工流程和关键参数。他设计制造的全新高性能夹具,可实现搅拌断针位置确定、残片数量精确定位与快速提取,不仅使工作效率瞬间提升3倍,而且修复合格率达到100%。目前,他和他的团队成员已先后完成10余次断针提取和缺陷修复,成功率为100%。他主导的斜台地板摩擦搅拌焊项目,不仅每年为公司节省上千万元的加工费用,也让陕飞公司成为国内首家掌握超大型构件摩擦搅拌焊技术的主机厂家。
飞机导管现场取样配制需要在飞机装配点和地面操作间两地往返,修配、比对、焊接、校形、试装配,现场导管取样与部装、总装工作高度交叉。针对空间狭小、作业人员多、时间紧等实际情况,黄卫带领队员开展突击攻坚,摸索出一套可调导管取样器和柔性导管拼装夹具,成功将导管取样过程缩短到20分钟,功效提高6倍,为公司节约工装制造成本50余万元。当出现斜台地板搅拌摩擦焊突发零件焊接缺陷时,黄卫与制造工程部、生产管理部技术专家携手攻坚,多次讨论、试验、排查,焊接试片40余片,排查设备关键部位10余处,最终完成了设备主轴更换,重新维护设备、焊接试片后,消除了零件焊接缺陷,为完成飞机交付任务赢得宝贵时间。
在导管数字化生产线建设中,为解决导管组焊加工过程数控调姿位问题,黄卫主持开展《导管类零件数控定位组焊技术的运用研究》课题,自主设计制作数控定位/检测装置,改变传统导管夹具设计理念,实现导管组焊接数字模型调姿定位,填补国内航空大直径导管组焊数字化、夹具数控化等领域的空白,极大降低了科研任务研制前期工艺装备的制造成本。
在黄卫的带领下,团队以解决零件加工、导管焊接、组件装配等技术瓶颈为突破口,累计设计制作了各类工装夹具200多套,完成了全员改善课题80余项,承担并完成了公司科研攻关项目23项,为公司创造价值2000余万元,累计申报国家专利技术28项,累计开展技能培训4860余人次,黄钰轩、刘家豪、李大江等多名优秀青年职工在一线创新工作中纷纷涌现出来……(文字/李磊 冯义党)
转载此文是出于传递更多信息目的。若来源标注错误或侵犯了您的合法权益,请与本站联系,我们将及时更正、删除、谢谢。
https://www.414w.com/read/1084807.html